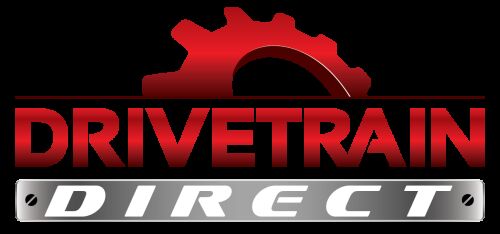
Head Studs, and Why They Matter
Mar 4 2025
What Are Head Studs & Why Do They Matter?
Head studs are threaded fasteners that secure the cylinder head to the engine block, similar to traditional head bolts. However, unlike bolts, studs are installed into the block first, and then the head is placed on top before securing it with a nut. This design provides multiple advantages, including improved clamping force and easier assembly.
Head Studs vs. Head Bolts: The Key Differences
Feature |
Head Studs |
Head Bolts |
Clamping Force |
More even distribution |
Can create uneven stress |
Installation |
Installed first, then torqued down |
Installed & torqued in one step |
Reusability |
Often reusable |
Typically one-time use |
Performance |
Preferred in high-stress applications |
More common in stock engines |
One of the biggest benefits of head studs over traditional bolts is the ability to achieve more precise and consistent clamping force. This is especially important in high-performance engines where extreme pressure and heat can cause head lift, leading to blown head gaskets and reduced engine longevity.
How Head Studs Increase Engine Life
Engines experience massive amounts of heat and pressure, especially under boost or high compression. Without proper clamping force, cylinder heads can shift slightly under load, leading to gasket failure, coolant leaks, and loss of compression.
Key Benefits of Head Studs for Longevity:
- Even Clamping Force – Unlike bolts, which can create uneven stress as they twist during torquing, head studs provide uniform pressure across the entire sealing surface. This helps prevent head gasket failure and ensures consistent sealing.
- Reduced Cylinder Head Movement – Under extreme conditions, a cylinder head can lift slightly off the block, leading to compression loss and potential engine damage. Studs minimize this movement by securing the head in place more effectively.
- Improved Heat Resistance & Durability – High-performance head studs are often made from chromoly steel or even aerospace-grade materials, designed to withstand extreme heat cycles without stretching.
- Ideal for High-Boost & High-Compression Builds – If you’re running forced induction (turbo or supercharger) or a high-compression N/A build, head studs become almost mandatory to prevent head gasket issues. Given that many of today’s hard working diesel trucks are running forced induction, this is where we come into play.
Summit Racing highlights this exact benefit in their tech guide:
"Upgrading to head studs is one of the most effective ways to reinforce the head-to-block seal, especially in high-boost and nitrous applications where pressure spikes can exceed factory bolt tolerances." (Summit Racing Tech)
Material & Design Evolution Over Time
Early Head Stud Materials vs. Modern Alloys
Back in the day, head studs were often made from basic steel alloys, which, while strong, lacked the heat resistance needed for extreme applications. Over time, manufacturers have developed high-tensile-strength alloys that dramatically improve performance.
Common Head Stud Materials & Strength Ratings
Material |
Tensile Strength (PSI) |
Common Applications |
OEM Steel |
~120,000 PSI |
Stock engines |
Chromoly Steel (8740) |
~190,000-210,000 PSI |
High-performance street & race engines |
ARP 2000 Alloy |
~220,000-230,000 PSI |
High-boost/turbo & nitrous builds |
L19 & Custom Age 625+ |
~260,000+ PSI |
Extreme racing applications |
Today, brands like ARP, Manley, and Moroso push the limits of head stud strength and coatings, offering options that resist corrosion, stretching, and fatigue over thousands of heat cycles.
Drivetrain Direct uses ARP 2000 Head Studs for all of our Studded engine builds.
Jegs reinforces the importance of material selection, stating:
"The right head studs can make or break an engine build—choosing premium tensile strength alloys ensures your engine can handle extreme conditions without failure." (Jegs Tech)
Real-World Usage: OEM vs. Performance Applications
Factory Applications
Most OEM engines come with head bolts, and for daily-driven vehicles, they work just fine. However, for performance applications—especially boosted setups—head bolts may not provide enough clamping force, leading to failures over time.
When Should You Upgrade to Head Studs?
- If you’re adding boost or nitrous
- If you’re increasing compression (for N/A builds)
- If you’re running an aluminum head on an iron block (different expansion rates can cause sealing issues)
- If you want to extend the life of your engine and reduce maintenance
Final Thoughts: Are Head Studs Always Worth It?
For mild street builds, factory head bolts may be sufficient—but if you're pushing high horsepower, running boost, or looking for long-term reliability, head studs are a must.
Pros & Cons of Head Studs
Pros |
Cons |
More even clamping force |
Higher cost |
Reduces head gasket failures |
|
Withstands higher boost & compression |
In short, head studs are one of the best insurance policies you can buy for your engine. They keep everything locked down under extreme conditions, reduce maintenance headaches, and add longevity to your build. Whether you're looking at ARP, Manley, or another top-tier brand, investing in quality studs is a move that any serious builder won’t regret.
References:
- Summit Racing Tech Guide: Summit Racing
- Jegs Performance Guide: Jegs